
This is why it’s key to determine your information’s purpose before committing to a specific diagram type. Like quantitative data, there is a right and a wrong way to express qualitative data depending on what you try to do with it. This may include steps in a workflow, members of an organization, images, concepts, timelines, and much more.
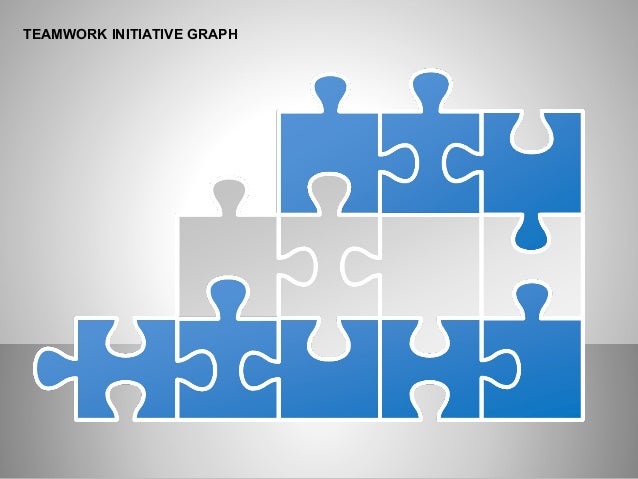
Qualitative data is any information that cannot be expressed with a numerical value or counted. 10 Types of Diagrams Examples for Your Teamġ0 Types of Diagrams Examples for Your Teamīefore we go any further here, let’s set something straight.That’s why you’re going to love this blog.Ĭonsider this article your new go-to guide for the top 10 diagrams you need to know for any type of workflow, including when to use them, examples, real-life testimonials, and must-have tricks for making them fast. Whereas qualitative data (information not defined by a single number) is better represented by diagrams like Mind Maps or Gantt Charts.īoth are key to the success of any healthy business, but sometimes, coming up with the right diagrams to best convey qualitative information is tough. Numerical information is represented by things like columns, line graphs, bar charts, or-my personal favorite-pie charts. That’s where graphs and diagrams come in handy. Whether your information is qualitative or quantitative, we need to look at these items as separate entities to understand them properly. While fighting tooth and nail through middle school, this was the mantra to live by, and even now, this sentiment still rings true when it comes to many things in life.īut that’s the point! We now know quality and quantity are necessary and constant elements of life.
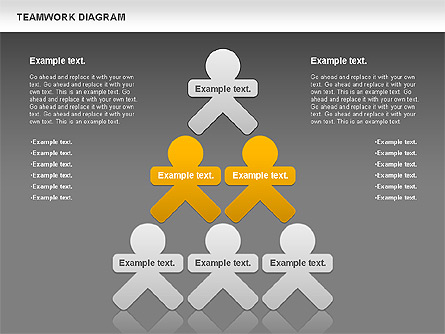
Please remember there is not a good approach to create plenty of sub-causes levels.We’ve all heard the phrase quality over quantity, right? For example insufficient temper can be caused with insufficient amount of carbon, low temperature during hardening process, etc. You can use this method for sub-causes specification, it means to analyze specified causes and look for causes of the causes. If it is detected you should look for new causes, relation among causes, etc. If the problem is not detected again you have found the root cause. Check the re-occurrence of the problem.use the Pareto analysis to prioritize the causes solution.Add data from the reporting system or dashboard (if they are available) to analyzed causes.Analyze the causes with the highest weight factors.When all of your ideas and possibilities are exhausted, let’s every member of your team to evaluate the causes with weight factors.Define potential causes, a brainstorming can used, and add them to relevant bones, as well called as general areas.Add branches (bones) to the backbone and write down general areas, the causes can occur from:.Draw a horizontal line from the rectangle as a fish’s backbone. Draw a rectangle on the sheet and write into a problem to be solved.Prepare a team of colleagues who are somehow interested in the problem.It is useful to use more colors for each area or for the most probable causes. Prepare for yourself a big sheet of paper, the Ishikawa chart you will draw on it.

There is an effect at the beginning, which has already happened or might happen as a potential and we would like to avoid its formation. To be able to identify the problem’s solution, the causes are demonstrated into the chart.ĭuring the Ishikawa diagram creation the brainstorming method shall be used in order to help us to specify all, even low probable, causes of solved problem. If you are not able to start a car it can be a set of causes – flat battery, shortage of fuel, imperfect plugs, electrical circuit shortage, broken central control section, etc. It is based on the basic principle – each and every effect (a problem) has its cause or combination of causes. Not any consulting should not avoid use it for looking for the problem causes and nonconformities nowadays. Just this diagram is very often used in the quality discipline. The diagram is sometimes called the Fishbone diagram for its appearance. The diagram has been described and implemented by Kaoru Ishikawa. Ishikawa diagram is a cause-and-effect diagram, its purpose is to find the most probably cause of problem being solved. The quality of products and services cannot be improved unless we have found the real cause of the faults being generated. The Ishikawa diagram is a diagram of causes and their effects aimed at finding the most likely cause of the problem being solved.
